1.8550 (34CrAINi7) steel is designed to be used in applications requiring high corrosion, temperature, wear, and fatigue resistance. It is a nitriding steel commonly alloyed with chromium, aluminum, nitrate, and molybdenum, which allows for achieving a surface hardness of at least 950 HV after nitriding. It is widely used in energy, machinery, and automotive industries when in the heat-treated condition.
1.8550 (34CrAINi7) steel finds wide application in general engineering, such as non-welding screw, rod end, cylinder, piston, gear, extruder, and segment manufacturing, plastic extrusion machine screws and barrels, all kinds of shafts, machine parts, and plastic injection molds.
Chemical composition % of steel 34CrAlNi7-10 (1.8550): EN 10085-2001
C | Si | Mn | Ni | P | S | Cr | Mo | Al |
0.3 – 0.37 | max 0.4 | 0.4 – 0.7 | 0.85 – 1.15 | max 0.025 | max 0.035 | 1.5 – 1.8 | 0.15 – 0.25 | 0.8 – 1.2 |
Mechanical properties of steel 34CrAlNi7-10 (1.8550)
Nominal thickness (mm): | 16 – 40 | 40 – 100 | 100 – 160 | 160 – 250 |
Rm – Tensile strength (MPa) (+QT) | 900-1100 | 850-1050 | 800-1000 | 800-1000 |
Nominal thickness(mm): | 16 – 40 | 40 – 100 | 100 – 160 | 160 – 250 |
Rp0.2 0.2% proof strength (MPa) (+QT) | 680 | 650 | 600 | 600 |
KV – Impact energy (J) (+QT) | +20° 30-35 |
Nominal thickness (mm): | 16 – 40 | 40 – 100 | 100 – 160 | 160 – 250 |
A – Min. elongation at fracture (%) (+QT) | 10 | 12 | 13 | 13 |
Brinell hardness (HB): (+A) | 248 |
Partial part type display:
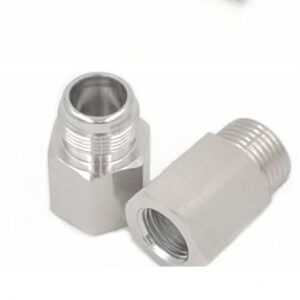
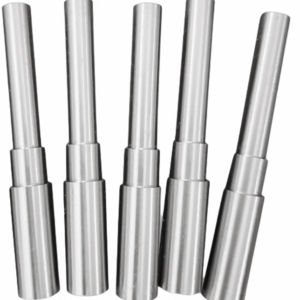
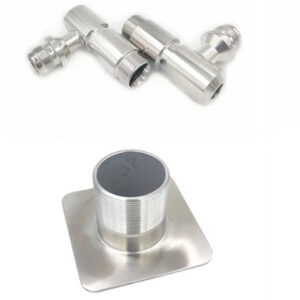
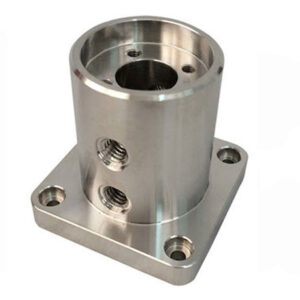
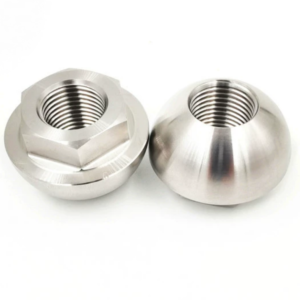
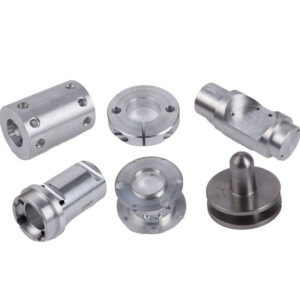