1.2085 stainless steel is a martensitic grade of stainless. It is magnetic and hardenable with rust resistant properties. 1.2085 stainless is characterised by having a 0.28-0.38 carbon, and 15-17% chromium content. This mix of analysis gives 1.2085 stainless steel an outstanding corrosion resistance and exceptional wear properties after heat treatment. Superior to 410 and 416 type stainlesses for most applications. 1.2085 stainless steel has good ductility in the annealed condition, but is capable of achieving 55HRC after treatment. Optimal corrosion resistance is realised when 1.2085 is surface ground and polished after hardening.
Applications of DIN 1.2085 Grade Material Grade steel 1.2085 is widely used in various industries due to its excellent properties.
1. Plastic Molds and Dies: 1.2085 steel is extensively used in the manufacturing of plastic molds and dies due to its high hardness and wear resistance properties. It is also resistant to corrosion, which makes it suitable for use in harsh environments.
2. Automotive and Aerospace Components: 1.2085 mold steel is used to manufacture various components for the automotive and aerospace industries, such as engine parts, suspension components, and landing gear components. Its high hardness and wear resistance properties make it suitable for use in these applications.
3. Medical Equipment: Steel material 1.2085 is used to manufacture various medical equipment such as surgical instruments and dental tools. Its corrosion resistance properties make it suitable for use in these applications.
4. Cutting Tools: 1.2085 tool steel is used to manufacture cutting tools such as knives and blades due to its high hardness and wear resistance properties.
5. General Engineering Applications: steel 1.2085 is also used in various general engineering applications such as shafts, gears, and bearings, where its high hardness and wear resistance properties are required.
Chemical Composition
C % | Si % | Mn % | P % | S % | Cr % | Ni % |
0,28 – 0,38 | max 1,00 | max 1,40 | max 0,030 | 0,050 – 0,100 | 15,00 – 17,00 | max 1,00 |
Mechanical Properties
1.2085 Mechanical Properties at ambient temperature | ||||||
Condition annealed. Quenched and tempered 850°C 0.2% Proof Stress: 905 Nmm² Tensile Strength: 950 – 1100 Nmm² Elongation: 10% Notch Impact Energy: (ISO-V) (J) 20 Hardness HB Max 230 |
Partial part type display:
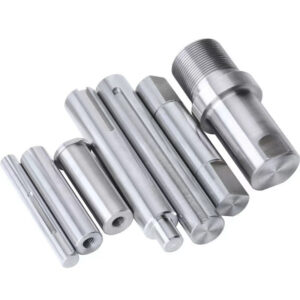
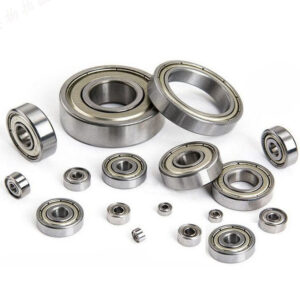
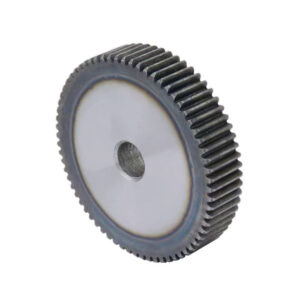
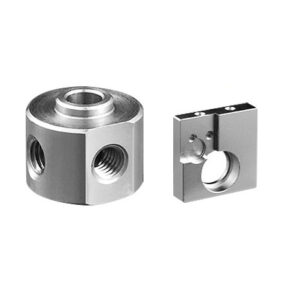
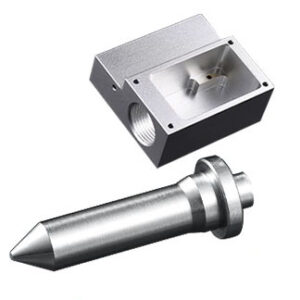
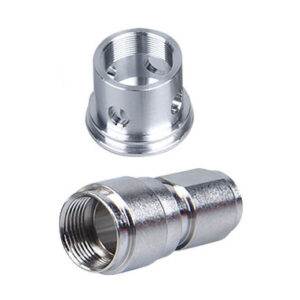